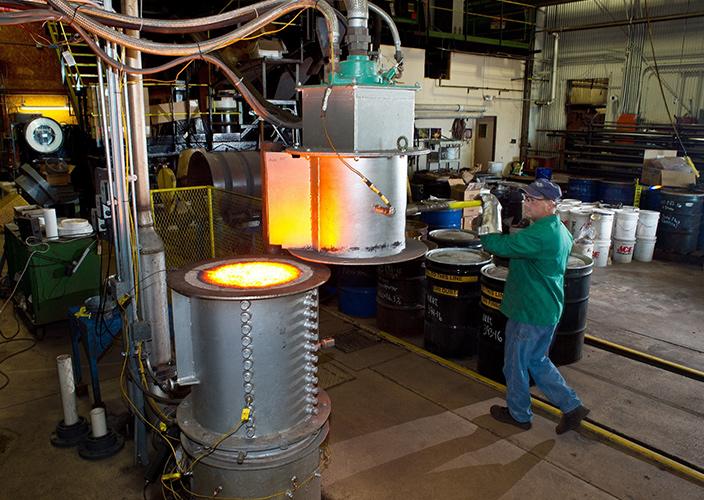
Program overview
NRRI’s Metallurgy program focuses on Minnesota’s ore bodies to understand the most optimal process for extracting metals for a variety of iron products, from pellets to briquettes. NRRI can fully replicate taconite mine pelletization processes on a pilot scale to develop efficiencies and improved products.
NRRI utilizes two pilot-scale metallurgical processes:
- Pyrometallurgy utilizes high temperatures up to 3,500 degrees Fahrenheit.
- Hydrometallurgy utilizes aqueous solutions to recover metals from ores, concentrates, and recycled or residual materials.
Metallurgy Capabilities
Agglomeration
Concentrates are typically blended with a binder before formed into small balls (agglomeration) using pelletizing techniques. Agglomeration equipment includes:
- Bench scale balling tire (airplane tire)
- Pilot scale disc pelletizer
Induration / Pelletizing
NRRI possess both a “mini-pot” and “pot grate” furnaces for induration testing.
Mini-Pot Testing
The Mini-Pot test can be performed several times per day to assess the drying, pre-heat, and firing zones of the induration furnace. The Mini-Pot can receive 1.5 Kg batches of green balls and fire them at temperatures up to 1350 C. Fired pellets can be used to test physical characteristics such as cold compressive strength, drop number, tumble index and abrasion index.
Pot-Grate Testing
The fully automated Pot Grate furnace at NRRI can be used to directly simulate straight grate furnaces and also provide representation of grate kiln furnaces. Pot Grate tests can be performed one time per day to assess the drying, pre-heat, and firing zones of the induration furnace. The Pot Grate can receive 136 Kg batches of green balls and fire them at temperatures up to 1350 C. Fired pellets can be characterized to understand their physical and metallurgical properties
Sintering
The fully automated Sinter furnace at NRRI can be used at varying bed depths to evaluate an ores ability to produce sinter. Sinter tests can be performed one time per day to assess the complete firing cycle of a sinter furnace. The Sinter furnace can be operated at temperatures up to 1250 C. Sintered material can be characterized to understand its physical and metallurgical properties.
Reduction
Related News

Pilot-scale, vertical mill from Switzerland is ‘game-changer’ for industry decarbonization efforts.

NRRI's minerals and metallurgy program in Coleraine, Minn., attracts global talent.