A crucial step in mineral processing – and in Minnesota’s iron ore processing – is comminution, a process of crushing and grinding. Large rocks must first be crushed and then ground down to tiny particles to expose the valuable or desired minerals so they can be separated from the waste rock. The prevalence of low-grade and complex ores make fine and ultra-fine grinding a necessity.
But this comminution process alone consumes about 40 percent of the total energy used in mining operations. It also accounts for at least 4 percent of total electrical power used globally. That’s thousands of terawatt-hours – a huge number.
There’s a better way, and now NRRI researchers have the technology to help the iron industry adopt this more efficient way of grinding. An agreement with Swiss Tower Mills (STM) Minerals for a VRMmill™ pilot vertical stirred grinding mill technology at the NRRI Coleraine site elevates the lab’s capabilities to world class.
“This is a game changer for our iron ore clients,” said Jestos Taguta, NRRI Senior Minerals Processing Engineer. “It’s a very mature technology but hasn’t had much application in the iron industry, especially in Minnesota. But this is where the world is going.”
The STM vertical stirred grinding mill can be used for coarse, fine and ultrafine grinding applications, while adding flexibility in flowsheet design and process development. Coarse particle processing has the potential to help Minnesota iron ore mining companies meet stringent environmental, social and governance standards.
Old mills are out
The traditional process for grinding taconite to a pulverized powder involves a ball mill – steel grinding balls tumbled in a large horizontal cylinder. The mills are huge, often greater than 20 feet long with a diameter of more than 14 feet and turning them takes a lot of energy. Ball mills are inefficient for fine grinding because they rely on dropping steel grinding balls on small particles to break them, referred to as impact grinding.
Stirred mills, on the other hand, overcome the inherent limitations of ball mills with a vertical rotating mill shaft equipped with grinding rotors. Smaller ceramic grinding media is used for the so-called attrition grinding which is more than 30 – 40 percent more energy efficient.
But what’s especially unique at NRRI is coupling this technology with a High-Pressure Grinding Roll (HPGR). This Weir Minerals HPGR can be used upstream in the comminution process to crush the larger rock particles into smaller sizes.
Industry experts realize that the transformative mineral processing flowsheet of the future will include emerging, energy efficient technologies like the HPGR and vertical grinding technologies. Utilizing energy efficient technologies such as these align in NRRI’s research with our goal of decarbonizing the iron and steel industry.
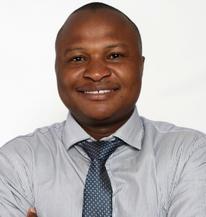
“I have been to a number of R&D facilities world-wide and none of them have both technologies under one roof,” said Taguta. “This gives us a very strategic position, globally, to design and demonstrate innovative and sustainable mineral processing processes and flowsheets.”
New mills are in
Along with this loaned pilot-scale vertical mill, NRRI is purchasing a small-scale version of the same mill for bench testing and proof-of-concept studies. It will allow researchers to test samples of less than 100 kilograms.
NRRI testing of the STM vertical mill for U.S. Steel’s Keetac plant led to the upgraded equipment purchase and successful energy efficiency savings for the plant. NRRI has also heard from other iron ore clients that having this testing capability is crucial to their process improvements.
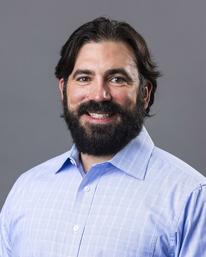
“Swiss Tower Mill saw the value in us having this technology on the Iron Range, which is why they partnered with NRRI to put a pilot-scale mill in Coleraine,” said Matt Mlinar, Mineral Processing and Metallurgy Research Group leader. “Because it reduces energy use, this is an important part of our strategic effort to help the iron and steel industry reduce their carbon emissions.”
After crushing and grinding, separation of the valuable minerals from waste rock is achieved using magnetic, gravity separation and flotation. NRRI is also investing in emerging coarse and fine particle flotation technologies to increase metallurgical, water and energy efficiencies.
“Our clients will definitely benefit from the synergism between these various cutting-edge, sustainable and energy efficient technologies,” Taguta added.
Logistics
The international transport of the vertical mill had NRRI’s Technical Operations team working extra hard to get the equipment from Austria to Coleraine. New equipment installation always requires a number of technical, safety and quality checks, but the commissioning went smoothly with the help of STM representatives working directly with NRRI’s research support team on-site.
“Our Technical Operations, Safety, Quality and Finance teams played a large and important role working with STM and NRRI researchers to ensure the equipment meets our technical operating requirements,” said Technical Operations Director Kevin Kangas. “NRRI continues to build solid long-term relationships with many collaborators that serve industry’s current and future needs.”
PHOTO TOP: The commissioning team stands by the newly installed STM VRMmill™. From left: Paul Mack (NRRI), Michael Moser (STM), Kyle Bartholomew (NRRI consultant, Metcom, Inc.), Fisher Wang (STM), Jeff Kinkel (NRRI) and Samantha Harbin (NRRI).